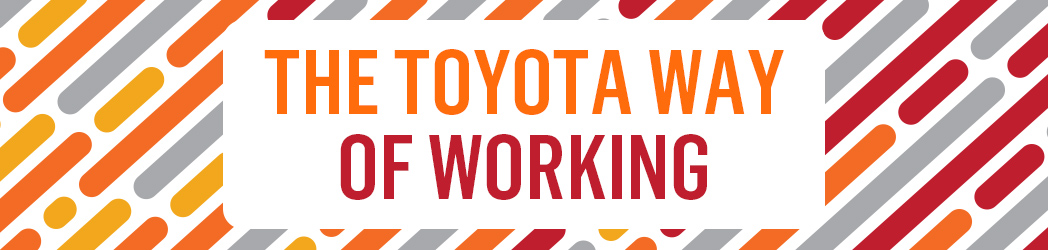
How Does Toyota’s 5S Process Improve Any System?
Who among us doesn’t want to be more organized? In addition to improving productivity and efficiency, precise standardization contributes to a more serene experience, reducing stress and improving our mood and how we function.
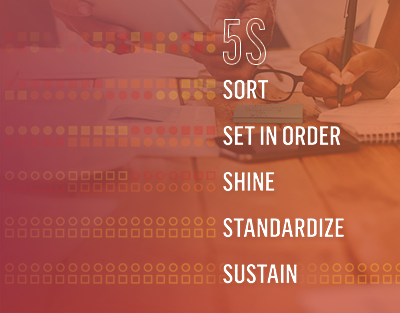
The 5S philosophy is foundational for Kaizen and the Toyota Production System and is woven within Toyota Industries Commercial Finance (TICF) to advance the team’s success. This process can be launched in any context: a business setting such as a personal office or shared meeting space, a manufacturing or warehouse facility, a retail, restaurant, or healthcare site, or even your own personal space at home.
The discipline is based on five words starting with the letter “S.” The principles in Japanese and English are:
-
- Seiri (Sort)
- Seiton (Set in Order)
- Seiso (Shine)
- Seiketsu (Standardize)
- Shitsuke (Sustain)
The goal of the system is to avoid waste, and it aims to eliminate unnecessary steps and avoidable spending. The process is of crucial importance because it also contributes to fewer mistakes and safety hazards.
Here are the phases of the 5S process:
-
- Sort: Separate items into three categories—necessary, unnecessary, and unknown—to determine which ones belong in your workspace, closet, desk, or other relevant area.
- Set in Order: Remove unnecessary items and properly arrange the remaining items in their optimal position.
- Shine: Clean the area, inspecting as you go, which will make it easier to identify abnormal or unsafe conditions in the future.
- Standardize: Make sure the placement of items complements your workflow, then document standardization rules so you can duplicate this optimized process and easily share the guidelines with team members.
- Sustain: Commit to the self-discipline to ensure that items are in their proper place every time until it becomes a habit.
When properly implemented and adhered to, the 5S approach supports our associates and the company by decreasing waste and improving efficiency and safety.
Recent Comments